Pile Driving
Our Pile Driving Services Include:
- Pipe Pilings
- Foundations
- Sheetpiling
Pipe Pilings
A vibratory pile driver literally fluidizes the lake bottom, allowing the piling to practically drop into place. In favorable conditions, a vibratory hammer can drive a piling to grade in a matter of minutes. In tougher conditions, such as hard clay, a diesel impact hammer is utilized to provide more driving force. In conditions such as limestone, it is often necessary to drill and grout the pilings in place.
For ten consecutive years, we installed and removed two pilings inside the breakwall off Burke Lakefront Airport for the Cleveland National Air Show to establish the “flight line” for the high performance planes. When the area was filled in by the Corps dike disposal, the makers were moved onto land.
Our Pile Driving customers include:
- The U.S. Coast Guard
- LeMarin Condominiums
- The Marina at the Westlake
- Edgewater Yavht Club
- Lakeside Yacht Club
- Cedar Point
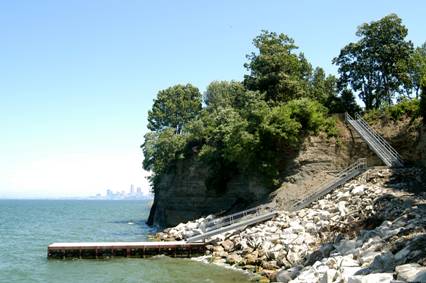
The most efficient method of installing pipe pilings is to use a vibratory pile driver mounted on an excavator or crane.
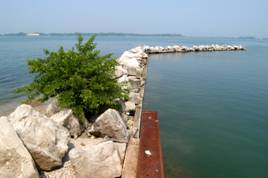
Foundations
Catwalks are often constructed as boathouse foundations. In 1992, we were hired by a group of homeowners on Bimini Drive in Sandusky after a fire consumed their boathouses. Our scope of work was performed in three phases.
Phase 1
The demolition and removal of the remains of 35 boathouses; salvage of the remains of vessels and removal of debris from the channel.
Phase 2
Surveying, dredging, and new sheetpile bulkheading and backfilling for 33 of the homeowners.
Phase 3
Construction of catwalks and fire walls for the boathouses for 33 of the homeowners prior to reconstruction of the houses.
Sheetpiling
Steel sheetpiling is utilized as a method of bank stabilization and allows for docking of boats. When properly designed and constructed, a sheetpile wall will outlast wood or concrete bulkheads and require the least maintenance. The corrosion rate for steel in fresh water is about 1/8” in fifty years in the absence of scouring. Ladders, dock fenders, cleats, lights and other appurtenances may be welded or potted to the structure.
“The most expensive system one can install is that which fails.”
What causes sheetpiling failure?
A disturbingly high percentage of steel sheetpile walls, particularly in the private sector, include structural failures. This is usually the result of inadequate design. Before a wall can be properly designed, it is mandatory that the water depth, soil conditions and design height of the wall be determined.
Most failures are due to insufficient sheet length (“short sheets”), an inadequate tierod/deadman system or welded as opposed to bolted connections.
A proper design should be engineered and let out for bids to qualified contractors. Experience, insurance, references, quality of workmanship and equipment must be considered.
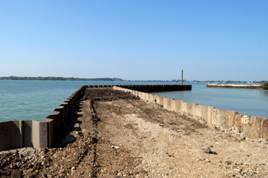
The most efficient method of installing pipe pilings is to use a vibratory pile driver mounted on an excavator or crane.
Related Projects
Marina Reconstruction
We reconstruct Battery Park Marina in Sandusky. The project consisted of demolition of the existing docks and stone filled cribs, closing the existing entrance with a sheetpile cell, excavation of a new entrance, construction of a breakwater extension and drilling and grouting of 15” diameter pipe piles into a limestone bottom for new floating docks.
Boathouse Foundations
We were hired by a group of homeowners on Bimini Drive in Sandusky after a fire consumed their boathouses. Our scope of work included 3 phases. 1) Demolition & Removal 2) Surveying, dredging, new sheetpile bulkheading and backfilling for 33 homeowners 3) Construction of catwalks and fire walls for boathouses.
Dredging
We were secured by US Army Corps of Engineers to dredge near unexploded Ordnance which peppered the mouth of the Toussaint River resulting from testing and fireproofing artillery in the early 1900s. The project was to determine a safe and efficient means to dredge such materials. Blast protection shields were built and installed to protect the crew. The material was dredged by clam bucket and placed on specially constructed screens which were affixed to the tops of the dump scows. Then a high powered fire hose was used to sift the dredge material through a screen, leaving any ordnance atop the screen. Video cameras were used to monitor the screens. An ordnance team from Human Factor Applications, Inc. worked with our crew, handling and disposing of any ordnance found.